
Typical inputs for industrial process workflows are energy, water, and other raw materials. Identifying the key inputs required to begin and run the process is an important step in process workflows.
Flow diagram iso#
The naming conventions laid down by ISO must be followed while naming the process. The process should be named to represent the essential aspects related to the process or the objective of the process. Here are the steps in documenting a process workflow: 1) Name the process: Once the workflow is documented it becomes easy to understand the workflow and identify the redundancies in it. Two main purposes of process workflows are explaining how the process works and improving process efficiency.ĭocumenting a process flow is the first step to understanding the process. Setting up the sales process, employee onboarding, and Capex approvals are examples of process flows. The steps in the workflows visually guide and indicate which stage of the process people are in. Process flows define a set of steps that employees can follow to achieve desired business outcomes. Well-defined process workflows help streamline and optimize business processes. Accountability of employees also improves as each employee is clear about the role, they play in the business process. The overall transparency of the process increases with a process workflow.Īssigning tasks to appropriate stakeholders becomes easy with a process flow. Identification of risks associated with the process is easier when you have a clear process flow.Įach team member gets clear insights into the status of tasks with an established workflow. Detection of opportunity gaps and taking measures to improve them becomes easy when you have a standard process workflow. Once you have a clear process flow, identifying redundant and repetitive tasks becomes easy. Internalizing the process and enabling future changes becomes easy when you have a standard flow. Training employees on the process flow is easy when you have established the flow clearly. Having a process design in place helps employees understand the flow. Including resources in the process flow design helps plan their utilization efficiently. Process flow creation helps identify the resource requirements of the process. The main benefits of creating a process flow are:Ĭreating a process workflow standardizes the operations so that employees get to work on established, time-proven processes. The tasks in process flows can either be executed in a sequential or parallel manner. The main aim of process flows is to streamline and standardize business processes and provide a better understanding of business to the team.
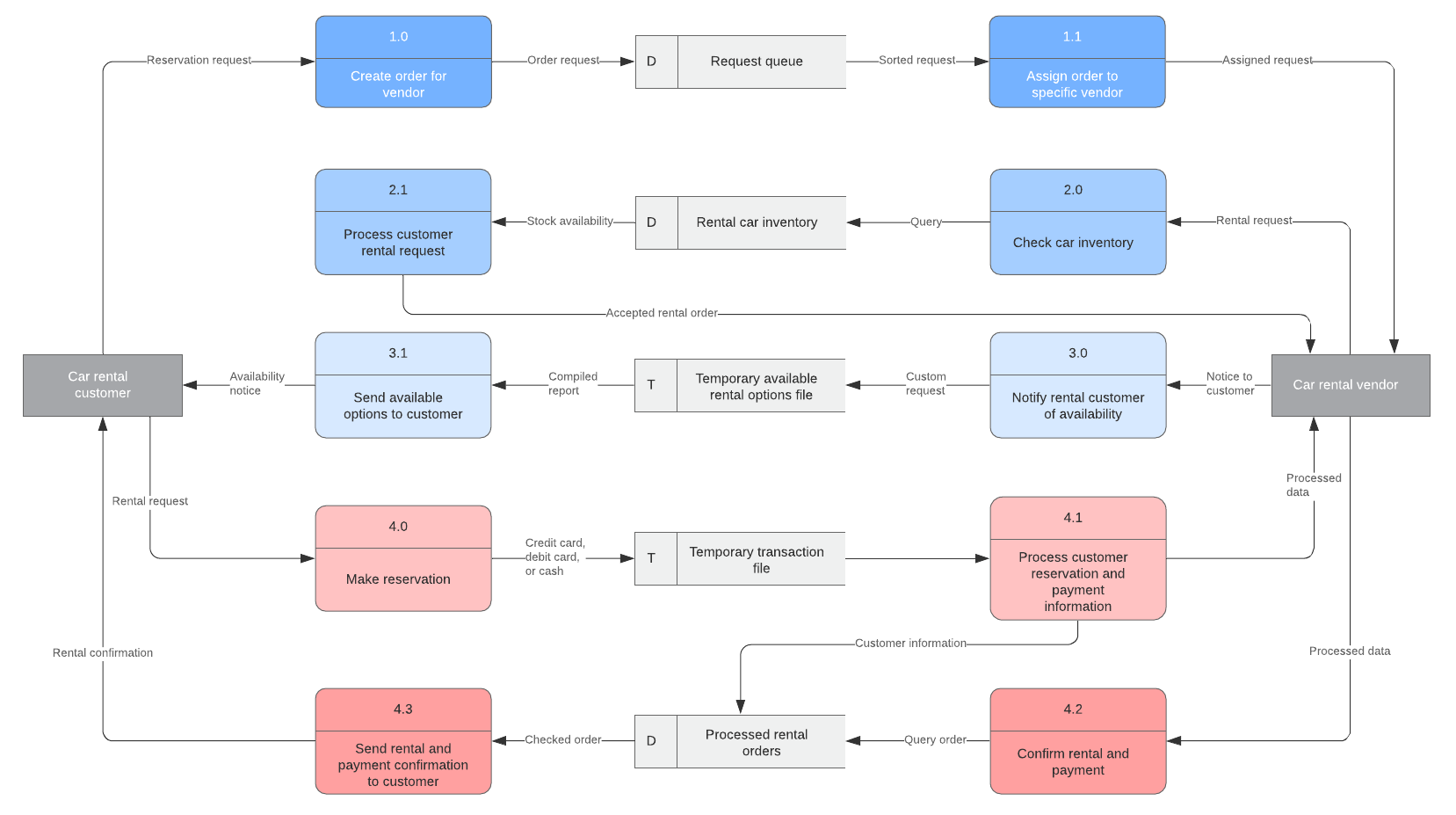

Process flow components include operations, timelines, resources, and people.
Flow diagram series#
The definition of process flows is a series of sequential tasks that guide people to get work done. A process flow represents the order in which tasks need to be executed in order to achieve business goals. Each task in the process flow is governed by input, transformation, and output. Process flows or workflows refer to a series of sequential tasks that are performed to achieve a certain goal. Understanding Process Flows through Flow Diagrams Business productivity is directly proportional to the efficiency of business processes. Improving the efficiency of business processes requires a complete understanding of the process flows.
